The LCS Story
The world's leading improvement qualifications and community
The world's leading improvement qualifications and community
The LCS helps Improvement Leaders to build capability and credibility, drive cultural change, and deliver measurable results, by offering a globally recognised qualification framework and access to the world’s leading professional improvement community.
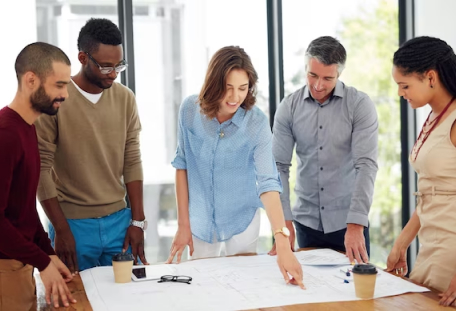
Created at LERC, Cardiff Business School
.png?width=106&height=106&name=CU%20-%20Logo%20-%20RGB_Cardiff-Logo-Red%20(002).png)
The LCS was launched in 2005 by the Lean Enterprise Research Centre (LERC) at Cardiff University, as a vehicle to help organisations develop staff Lean capability and adopt Lean thinking more effectively. In 2014 a new spin out company, Lean Competency Services Ltd., was awarded the Cardiff University licence to operate and develop the LCS.
This was managed and controlled by Simon Elias, former LERC director and chief architect of the LCS from 2005. Simon was LCS Director until October 2023 when he retired. LCS is now managed by Reinvigoration Group.
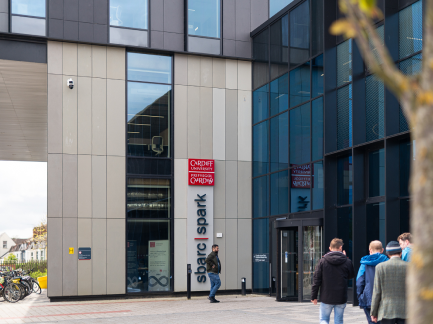
Why the LCS was created
LCS was developed by LERC in response to the lack of credible workplace-based Lean qualifications, which was inhibiting the development of staff Lean capability training. A system was developed, piloted and launched in 2005. It has since been adopted by private and public sectors in the UK and internationally, where it plays an important role in supporting Lean implementation and in creating a continuous improvement culture.
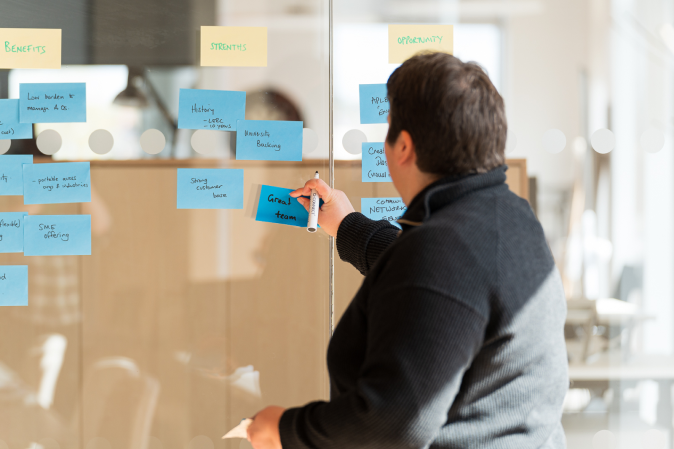
The Future of LCS
The LCS stands as the premier improvement qualifications framework, embraced by over 160 organisations worldwide and steadily gaining traction. As we extend our reach into new territories, we consistently showcase the value it offers to both organisations and individuals. Our aspiration is not only to deliver the foremost improvement qualifications framework but also to foster a dynamic community where like-minded organisations and professionals can network, share and learn from one another.
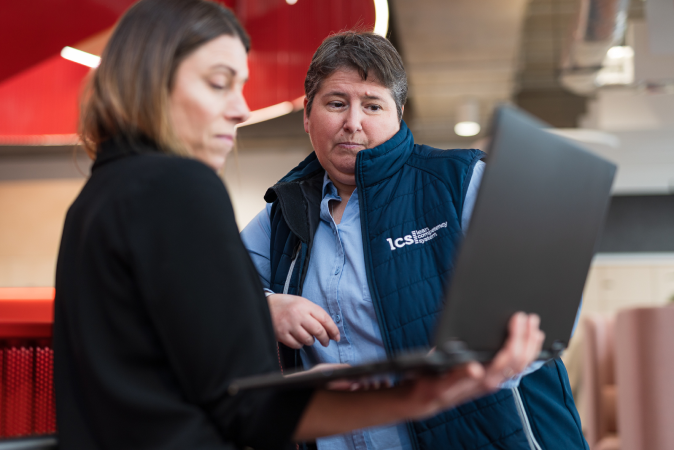